Film Faced Plywood
- Size: 1220*2440mm(4’*8′), 900*2100mm , 1250*2500mm or upon request
- Thickness: 9mm , 12mm , 15mm, 18mm , 21mm , 24mm or upon request
- Thickness Tolerance: +/-0.5mm
- Face/Back: Dynea dark brown film, black film, brown film, Anti Slip film , plastic film
- Core: Board Poplar, Eucalyptus, Combi, Birch or upon request
- Glue: Phenolic ,WBP,MR
- Grade: One Time Hot press / Two Time hot press / Finger-Joint
- Certification: ISO , CE, CARB , FSC
- Density: 500-700kg/m3
- Moisture: Content 8%~14%
- Water: Absorption ≤10%
Film Faced Plywood Factory - Dongstar® - China Formwork Plywood Manufacturer
Film faced plywood is a durable and versatile construction material. It is overlaid with a protective film on both sides, making it resistant to moisture, chemicals, and abrasion. This plywood is commonly used in concrete formwork due to its strength and reusability. It provides a sturdy platform for concrete pouring and ensures consistent results. Additionally, form plywood finds applications in various construction areas, such as walls, floors, and roofs. At Dongstar®, we are a reliable manufacturer and supplier of high-quality formwork plywood from China. Choose us for dependable products that meet international standards. Contact us to explore our range of options.
Core material
Plywood core materials play a crucial role in determining the strength, durability, and overall quality of the plywood.
The choice of plywood core material depends on the specific requirements of the application, considering factors like strength, stability, moisture resistance, and cost.

Finger Joint/Blockboard
Glue: WBP Melamine
Thickness: 12/15/18mm
Reuse: 2-4 times
Price: Cheap
Finger joint core is composed of smaller pieces of wood joined together with finger-like interlocking joints.
It offers excellent strength, stability, and resistance to warping or splitting.
Finger joint core is often used in high-quality plywood for applications that require superior structural integrity, such as construction, flooring, and furniture manufacturing.

Poplar
Glue: WBP Melamine
Thickness: 8/10/12/15/18mm
Reuse: 6-10 times
Price: Medium
Poplar core is made from the lightweight and straight-grained poplar wood.
It is known for its stability, ease of use, and affordability.
Poplar core plywood is commonly used in interior applications like cabinetry, paneling, and decorative projects where weight and cost are important factors.

Eucalyptus
Glue: WBP Melamine/Phenolic
Thickness: 12/15/18mm
Reuse: 10-15 times
Price: Premium
Eucalyptus core is derived from the fast-growing eucalyptus tree, known for its strength and durability.
It provides excellent stability, resistance to moisture, and high load-bearing capacity.
Eucalyptus core plywood is often used in outdoor and marine applications, including boat building, exterior construction, and infrastructure projects.
Glue Types
When it comes to plywood glue, two common types used for their superior bonding properties are WBP Melamine and WBP Phenolic.
WBP Melamine Glue:
WBP Melamine (Water Boiled Proof Melamine) is a synthetic resin adhesive.
It is known for its excellent water resistance and durability, making it suitable for exterior and marine applications.
WBP Melamine glue creates a strong bond that can withstand exposure to moisture, humidity, and changes in temperature.
It is commonly used in construction, concrete formwork, flooring, and other applications where plywood needs to withstand harsh environmental conditions.
WBP Phenolic Glue:
WBP Phenolic (Water Boiled Proof Phenolic) is a synthetic resin adhesive derived from phenol formaldehyde.
It is highly resistant to moisture, heat, and chemicals, making it ideal for both interior and exterior applications.
WBP Phenolic glue provides excellent bonding strength and stability, ensuring the plywood can withstand heavy loads and extreme conditions.
It is widely used in construction, furniture manufacturing, packaging, and other demanding applications that require durable and reliable plywood.
Both WBP Melamine and WBP Phenolic glues are engineered to meet stringent quality standards and provide long-lasting bonding performance. The choice between the two depends on the specific requirements of the project, including the intended application, environmental exposure, and desired durability.
Film Types
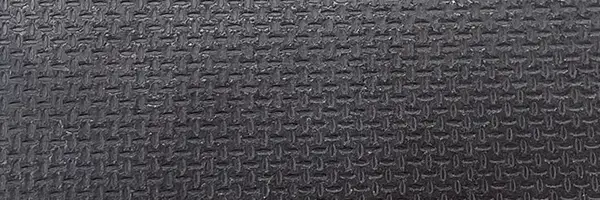
Anti-slip film
The special anti-slip film is usually used in the workshop to prevent the traffic of vehicles.
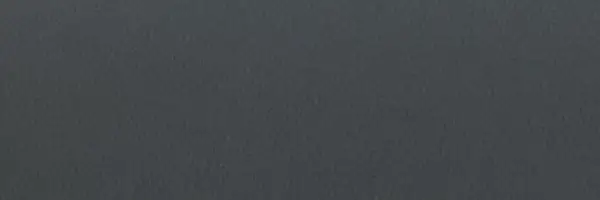
Black Film is a popular choice for film-faced plywood due to its high contrast and aesthetic appeal.
It provides a smooth and uniform black surface that offers good resistance against water, chemicals, and wear.
Black Film-faced plywood is commonly used in construction, concrete formwork, scaffolding, and other applications where a durable and visually appealing finish is desired.
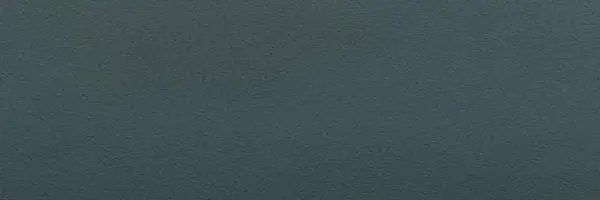
Brown Film is widely used in the construction industry for its durability and cost-effectiveness.
It offers good water resistance, strength, and protection against external elements.
Brown Film-faced plywood is suitable for various applications, including concrete formwork, flooring, roofing, and general construction.
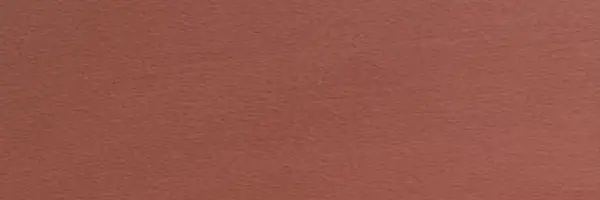
Red Film is known for its vibrant red color, which provides an eye-catching appearance to plywood.
It offers similar properties to other film types in terms of water resistance, strength, and protection.
Red Film-faced plywood is often used in construction, furniture manufacturing, and decorative applications where a distinct look is desired.
Edge Seal - Waterproof
Waterproof edge sealing is an essential step in plywood protection and longevity. It helps prevent moisture penetration and protects the edges from damage.
Remember, proper edge sealing is crucial to maximize the performance and longevity of form plywood, particularly in applications where exposure to moisture is expected. By taking the necessary precautions and using high-quality sealants, you can ensure the long-term durability and water resistance of your plywood products.
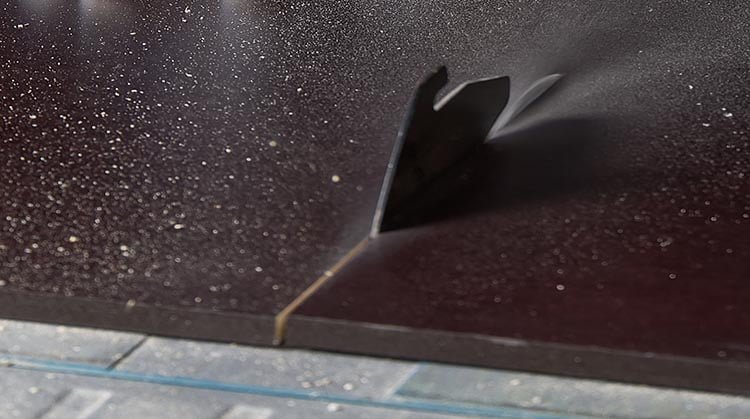
CONTACT US
We will answer your email shortly!
Don’t want to be tied down? Click to send email directly dongstarplywood@gmail.com
Form Plywood Applications
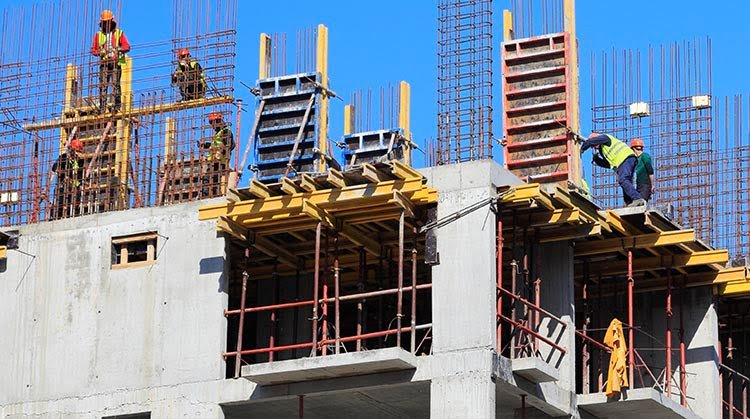
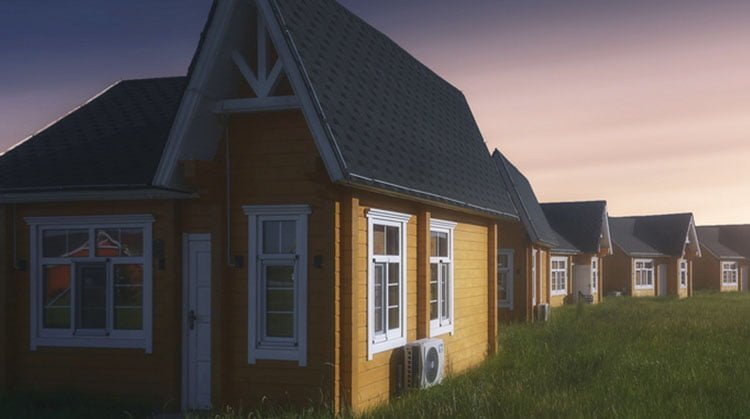
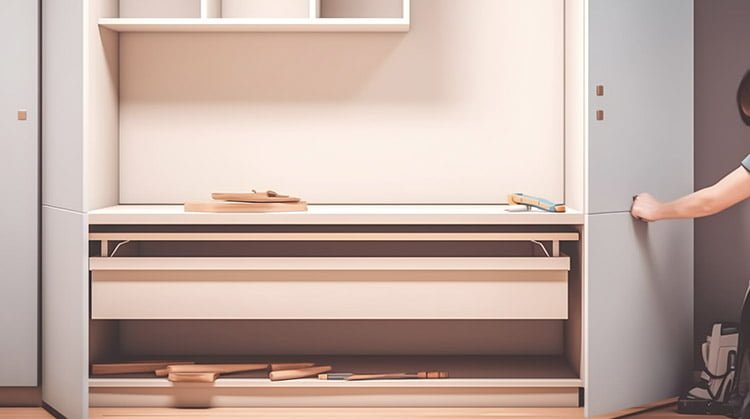