Particle board, also known as chipboard, is an engineered wood product that provides a cost-effective and versatile alternative to solid wood and plywood. Made from wood particles such as wood chips, sawmill shavings, and other wood residues bonded together using synthetic resin or glue under high pressure and heat, particle board has found widespread use in various applications due to its affordability and functional properties.
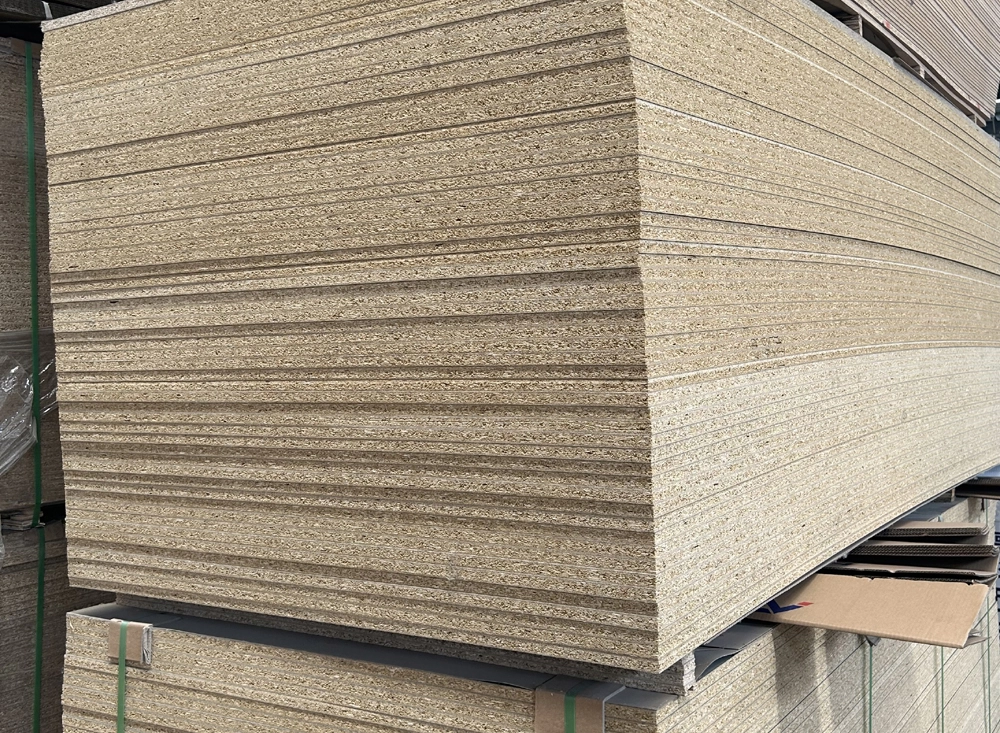
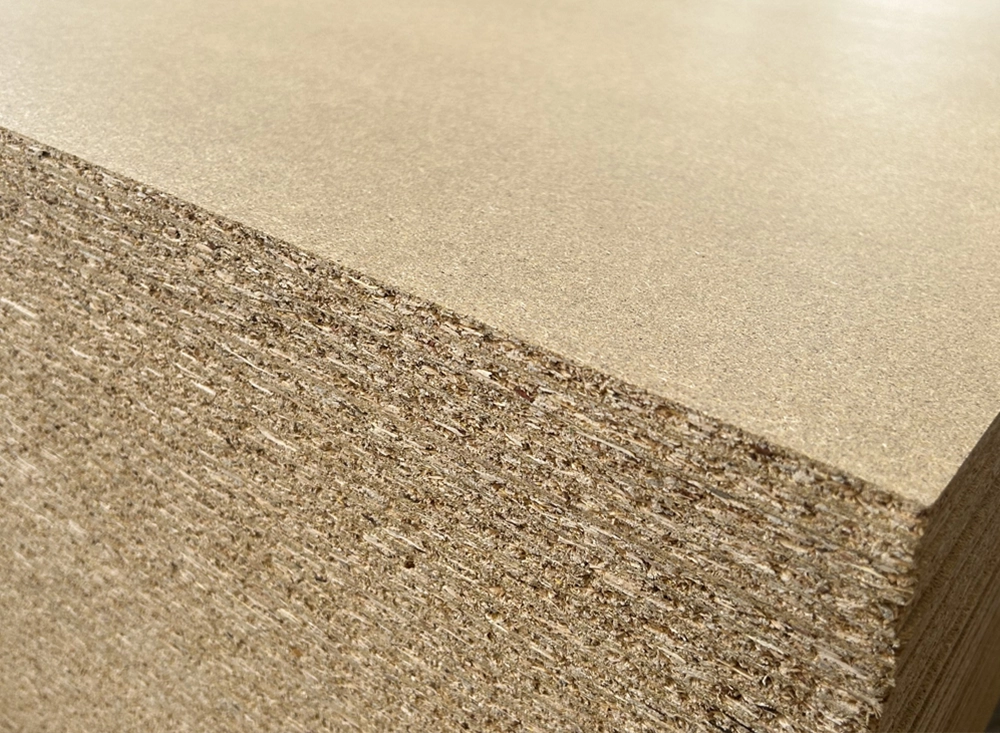
What is Particle Board?
Particle board, often referred to as chipboard, is a type of engineered wood product composed of wood particles such as wood chips, sawmill shavings, and other wood residues. These materials are bonded together using synthetic resin or glue under high pressure and heat to form a dense, flat sheet. It is a popular material in the furniture and construction industries due to its affordability and versatility.
History of Particle Board
The development of particle board can be traced back to the early 20th century, with significant advancements occurring during and after World War II. The need for efficient use of wood resources and the development of synthetic resins spurred the innovation and mass production of particle board. Over the decades, improvements in manufacturing techniques and adhesive technologies have enhanced the quality and applications of particle board.
Manufacturing Process of Particle Board
The manufacturing process of particle board involves several steps:
1. Collection of Raw Materials: Wood residues like chips, shavings, and sawdust are collected from sawmills and other wood-processing facilities.
2. Drying: The wood particles are dried to reduce moisture content, ensuring better adhesion and stability.
3. Mixing with Adhesive: The dried particles are mixed with synthetic resin or glue.
4. Forming: The mixture is formed into a mat.
5. Pressing: The mat is pressed under high pressure and heat to cure the adhesive and form a solid board.
6. Cooling and Trimming: The boards are cooled and trimmed to the desired dimensions.
7. Sanding and Finishing: The surface of the board is sanded smooth, and sometimes a veneer or laminate is applied for aesthetic purposes.
Types of Particle Board
There are several types of particle board, each designed for specific applications:
Standard Particle Board: Used in furniture and cabinetry.
Melamine Particle Board: Coated with a melamine finish for a durable, decorative surface.
Laminated Particle Board: Covered with a laminate veneer for added strength and aesthetics.
Moisture-Resistant Particle Board: Treated to resist moisture, suitable for areas with high humidity.
Advantages of Particle Board
Cost-Effective: One of the most affordable wood products available.
Versatile: Can be used in a variety of applications.
Uniformity: Provides a consistent surface without knots or grain variations.
Easy to Work With: Can be easily cut, drilled, and shaped with standard woodworking tools.
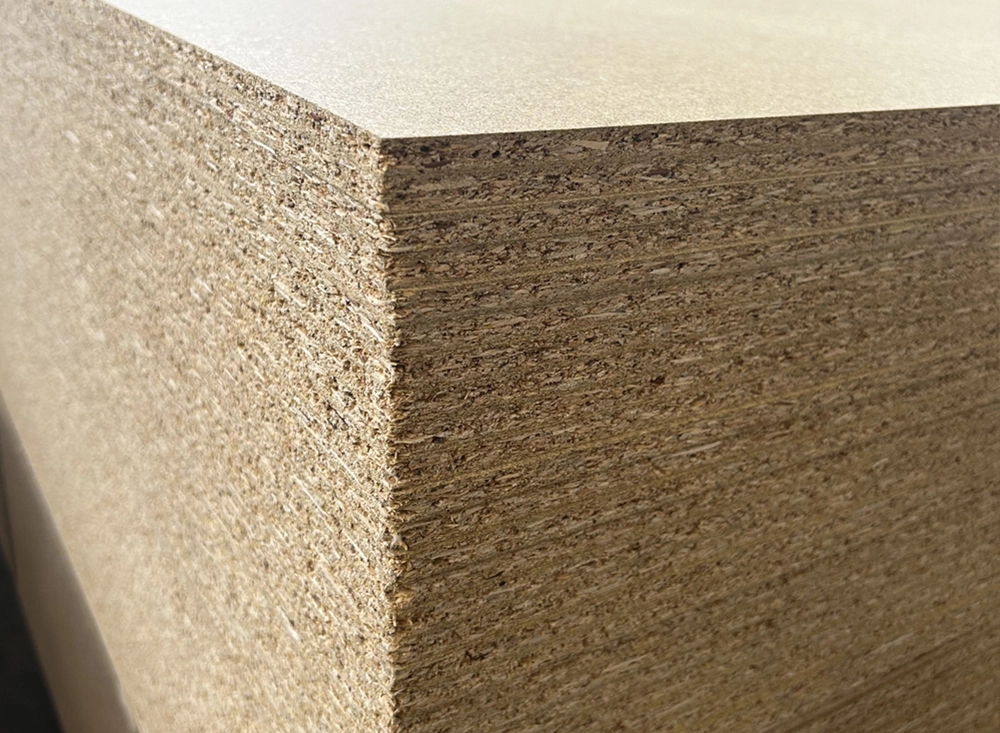
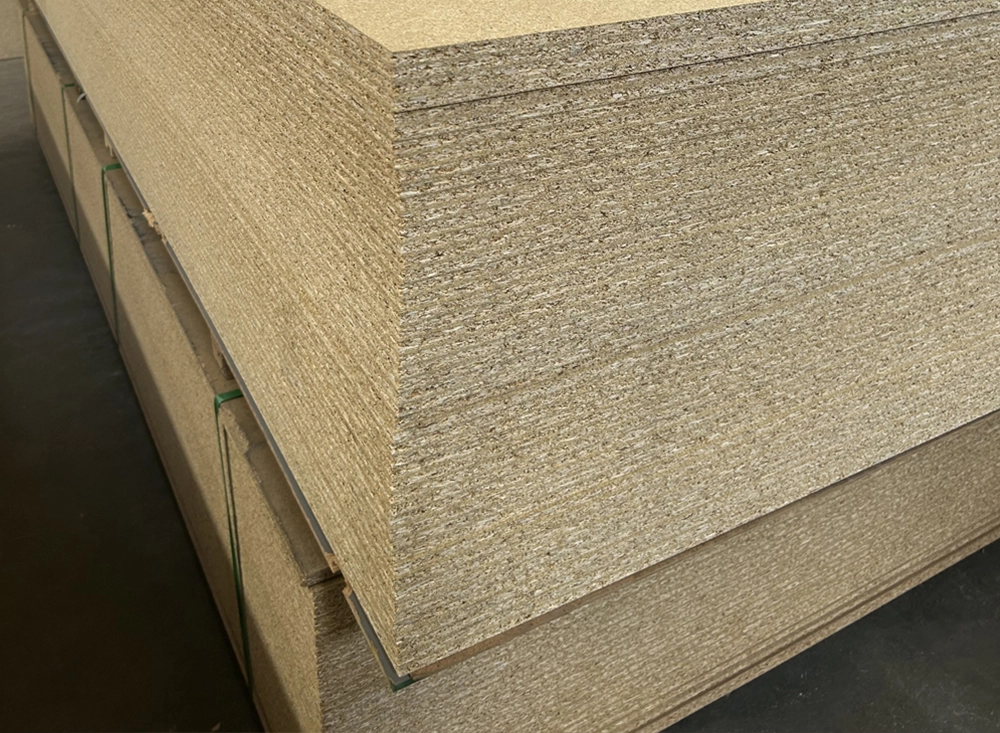
Disadvantages of Particle Board
Lower Strength: Not as strong as plywood or solid wood.
Susceptible to Moisture: Can swell and degrade when exposed to moisture.
Limited Aesthetic Appeal: Requires veneers or laminates for a finished look.
Environmental Concerns: Contains synthetic resins that may release formaldehyde.
Common Uses of Particle Board
Particle board is widely used in:
Furniture Manufacturing: Particularly in budget-friendly furniture.
Cabinetry: Often used for kitchen cabinets and shelving.
Flooring: Used as a subfloor materi.