Introduction to Oriented Strand Board (OSB)
Oriented Strand Board (OSB) is a type of engineered wood that has become a cornerstone in modern construction, particularly for its strength, versatility, and cost-effectiveness. Defined as a material made from compressed wood strands or flakes combined with adhesives, OSB is used extensively in both structural and non-structural applications. The creation of OSB represents a significant advancement in the use of wood resources, offering an alternative to plywood and other wood panels.
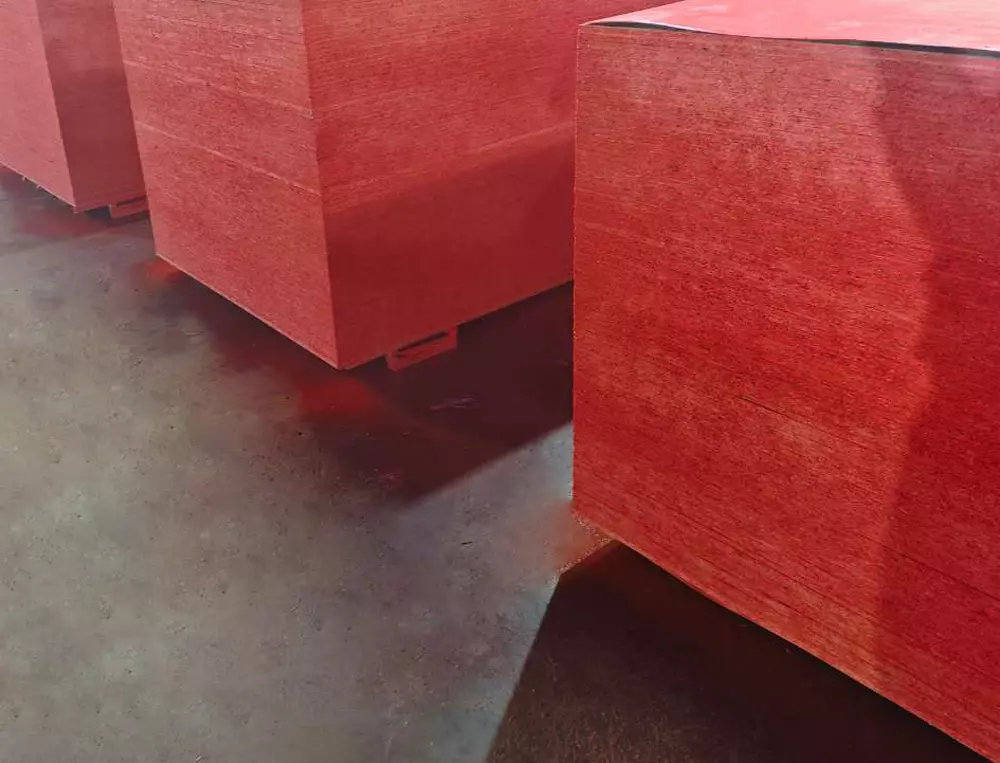
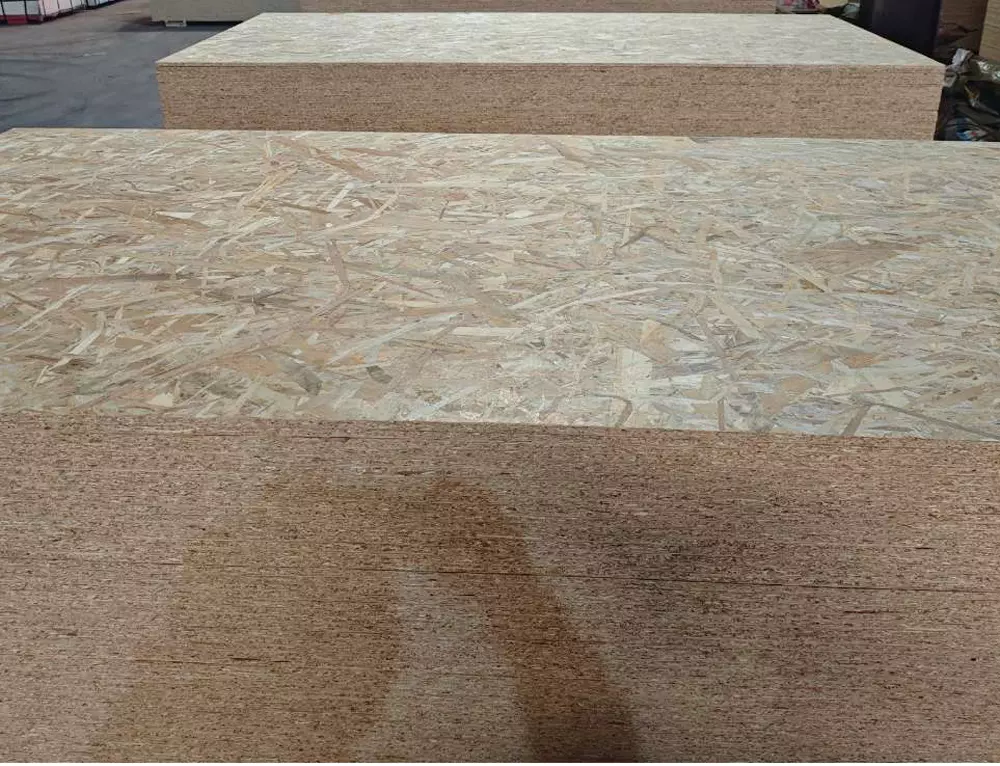
OSB emerged as a more uniform and economical alternative to plywood during the latter half of the 20th century. Since its introduction, OSB has grown in popularity due to its favorable mechanical properties, which are suitable for load-bearing applications such as flooring, wall sheathing, and roof decking. Its structure, which relies on the specific orientation of wood strands, gives it a high level of strength and durability, making it indispensable in construction.
The popularity of OSB has continued to rise as construction practices evolve, and sustainability becomes more critical. It plays a crucial role in various construction and industrial applications, offering an efficient and reliable material option. OSB’s widespread use in residential and commercial buildings highlights its importance in the construction industry.
Manufacturing Process of OSB
The production of Oriented Strand Board involves several stages, beginning with the selection of raw materials. The primary materials used are wood strands or flakes, typically sourced from softwoods like aspen, poplar, and southern yellow pine. These wood species are chosen for their availability, workability, and strength characteristics.
The manufacturing process starts with debarking the logs, which are then cut into strands. These strands are typically 3 to 4 inches long, 1 inch wide, and about 0.03 inches thick. The wood strands are then dried to reduce moisture content, which is crucial for bonding them with adhesives later in the process.
Once dried, the wood strands are coated with adhesive resins. These resins are vital to the performance of the final OSB product, as they provide the necessary bonding strength and influence the board’s moisture resistance. The strands are then aligned in specific orientations, with different layers placed perpendicular to each other. This cross-orientation is what gives OSB its high strength and stability.
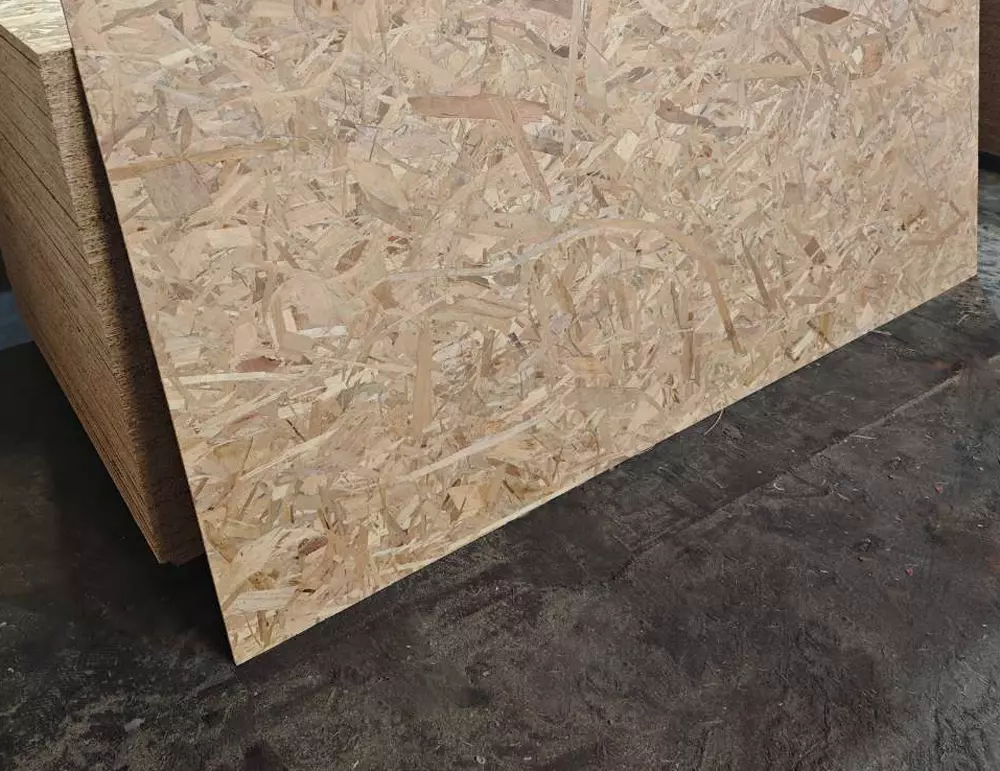
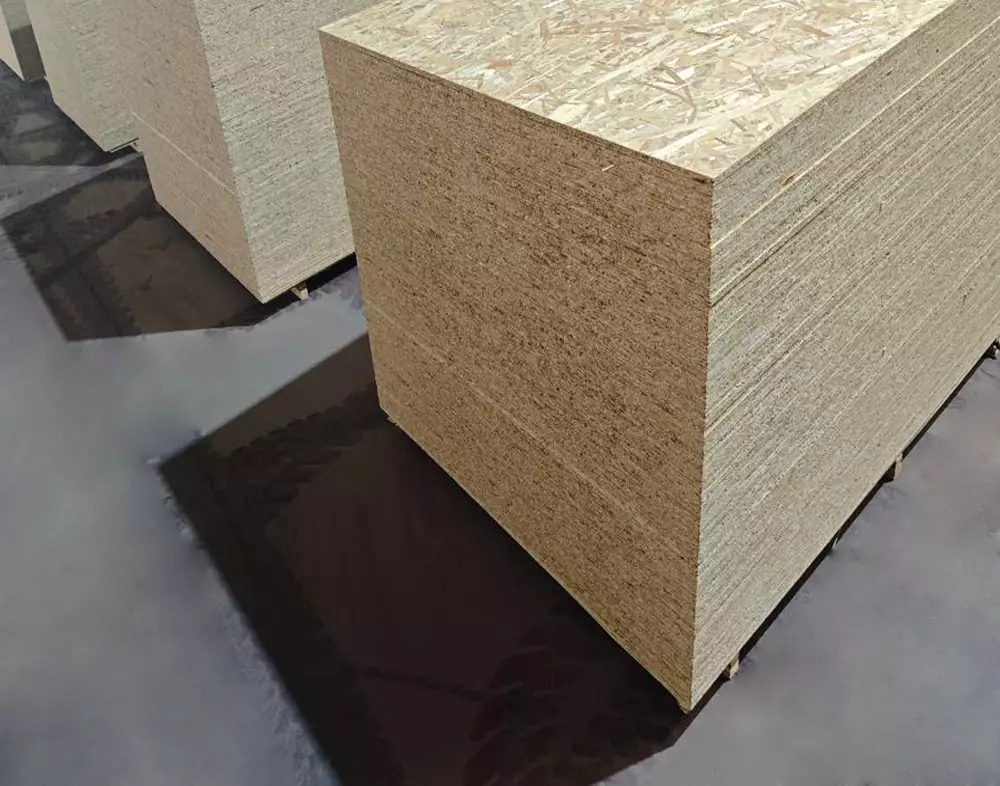
The layered strands are then subjected to high pressure and temperature in a press, which compresses the strands and cures the adhesive, forming a solid, dense board. The resulting OSB panels are then cut to size and may be sanded or surface-treated, depending on the intended use.
Throughout the process, quality control is maintained to ensure that the OSB meets industry standards for strength, durability, and performance. The entire manufacturing process is designed to maximize the use of wood resources, making OSB not only a strong and versatile material but also an environmentally friendly choice.